La sécurité logistique en entrepôt est essentielle pour protéger les travailleurs, les marchandises et les équipements. Entre manutention, circulation d’engins et stockage, les risques d’accidents sont nombreux. Pourtant, des règles simples permettent de limiter ces dangers et d’assurer un environnement de travail sécurisé.
Découvrez les mesures essentielles à mettre en place pour optimiser la sécurité logistique et prévenir efficacement les incidents en entrepôt.
- Organisation et aménagement de l’espace pour une sécurité logistique optimale
- Respect des obligations légales et réglementaires
- Formation et sensibilisation du personnel
- Bonnes pratiques en manutention et port de charges
- Sécurisation des équipements et des infrastructures
- Prévention des risques spécifiques en entrepôt
- Sécurité incendie et gestion des produits dangereux
- Assurer une sécurité logistique optimale
Organisation et aménagement de l’espace pour une sécurité logistique optimale
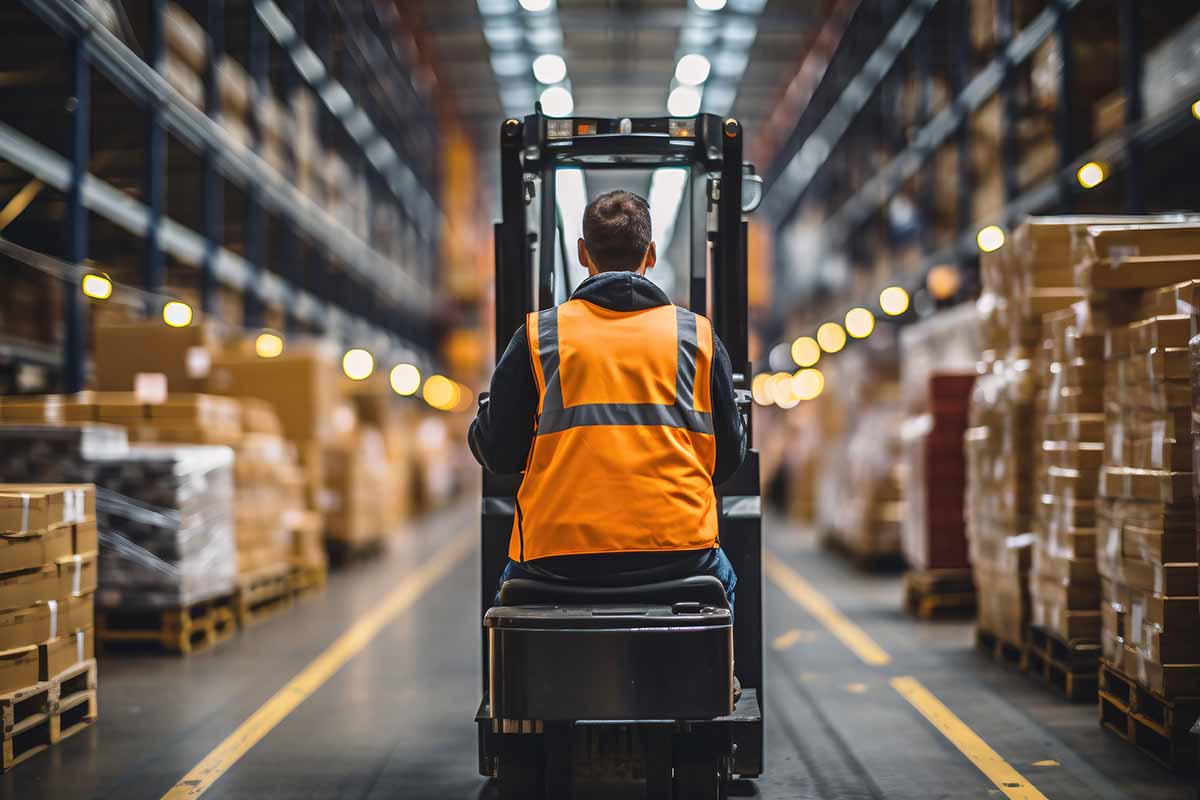
Une bonne organisation de l’entrepôt est essentielle pour garantir une sécurité logistique efficace. Un espace mal agencé peut entraîner des accidents liés aux collisions, aux chutes de charges ou aux déplacements imprévus d’engins de manutention.
Optimiser la circulation et les flux de travail
Une circulation bien organisée réduit les risques de collisions et fluidifie les opérations :
- Séparer clairement les voies dédiées aux piétons et aux engins motorisés.
- Définir des zones de circulation avec un marquage au sol visible et une signalétique adaptée.
- Maintenir une largeur minimale des allées (6 mètres) et une hauteur libre d’au moins 4,5 mètres pour les engins de manutention.
- Éviter l’encombrement des zones de passage en assurant un rangement optimal des marchandises.
Sécuriser les zones de stockage et de manutention
Un entreposage bien structuré prévient les chutes de charges et les accidents :
- Respecter les normes en vigueur pour l’installation des palettiers et des rayonnages (NF 15629).
- Vérifier annuellement la stabilité des structures de stockage avec un organisme spécialisé.
- Assurer l’accessibilité des produits pour éviter les manipulations risquées.
- Mettre en place des dispositifs de retenue pour éviter la chute des palettes et des marchandises.
Respect des obligations légales et réglementaires
Garantir une sécurité logistique optimale en entrepôt ne se limite pas à l’aménagement des espaces et à la prévention des risques. Le respect des obligations légales et réglementaires est indispensable pour assurer la conformité de l’installation et éviter toute sanction.
Autorisation d’exploitation de l’entrepôt
L’exploitation d’un entrepôt logistique est soumise à des réglementations strictes visant à prévenir les risques pour les travailleurs et l’environnement. Avant toute mise en service, une autorisation d’exploitation est requise, et elle est conditionnée par plusieurs critères :
- Respect des distances réglementaires : L’entrepôt doit être situé à une distance minimale de 20 mètres des zones d’habitation, des voies d’eau et des établissements publics (écoles, gares, routes).
- Conformité aux normes de construction et de sécurité : Les bâtiments doivent répondre aux exigences de solidité, de ventilation et de prévention des incendies.
- Déclaration aux autorités compétentes : Le responsable logistique doit s’assurer que l’entrepôt est déclaré auprès des services administratifs et respecte les normes en vigueur (ICPE, Code du travail, réglementation incendie).
Tenue d’un registre des matières stockées
Un suivi précis des marchandises entreposées est une obligation légale et un élément clé de la sécurité logistique. La tenue d’un registre des matières stockées permet de garantir la traçabilité des produits et de faciliter les contrôles en cas d’inspection.
Ce registre doit inclure les informations suivantes :
- Nature des produits : Classification des marchandises selon leur type (alimentaire, chimique, pharmaceutique, etc.).
- Emplacement des produits : Localisation précise des stocks pour une gestion efficace et sécurisée.
- Risques associés : Identification des dangers liés aux produits (inflammabilité, toxicité, réactivité) et mesures de précaution à appliquer.
Formation et sensibilisation du personnel
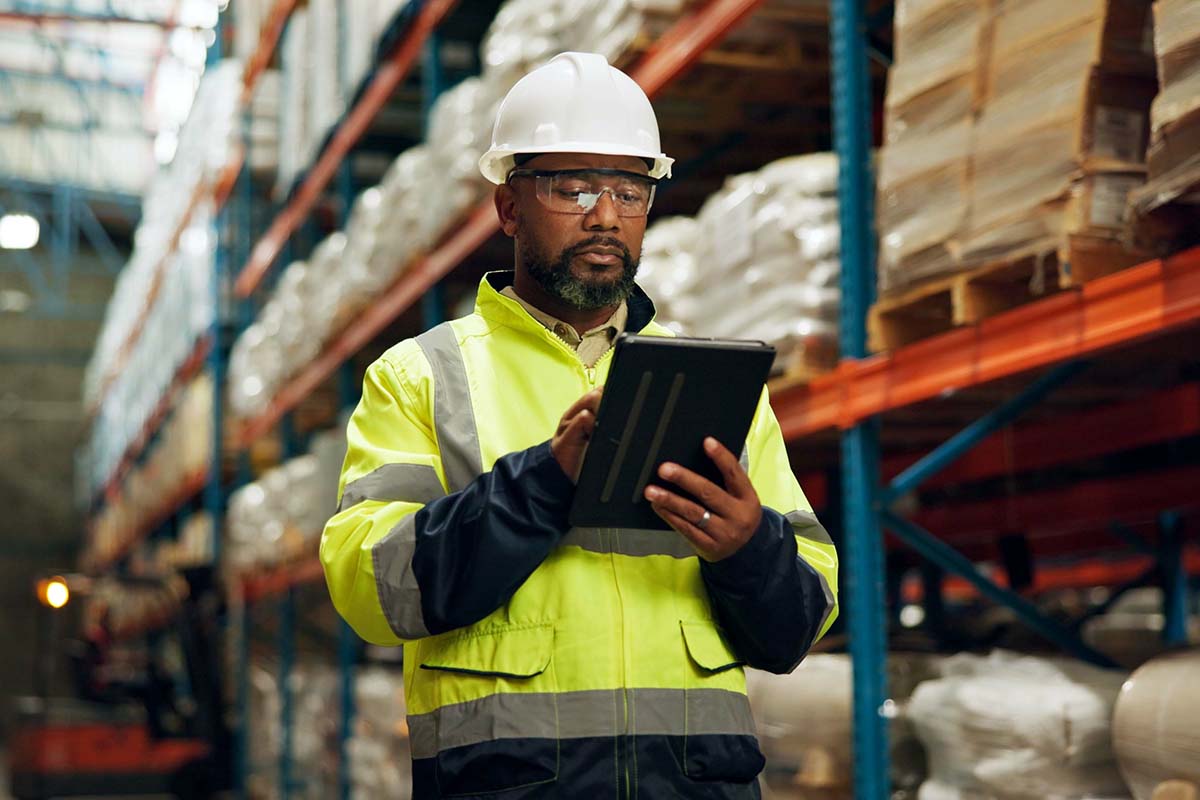
La sécurité logistique repose en grande partie sur la formation et la sensibilisation des employés. Un personnel bien informé et formé est capable d’identifier les risques, d’adopter les bons réflexes et de réagir efficacement en cas d’incident :
- Formation continue : Les risques évoluent avec les processus et les équipements. Organiser des sessions de formation régulières permet de maintenir un haut niveau de vigilance et de renforcer la sécurité logistique.
- Exercices pratiques : Mettre en place des simulations d’accidents permet aux employés d’appréhender les risques en situation réelle et d’adopter les gestes adaptés.
- Affichage et rappels visuels : Des panneaux de signalisation, des fiches de rappel et des consignes de sécurité clairement affichées facilitent l’assimilation des bonnes pratiques.
Une équipe sensibilisée est plus apte à réagir rapidement et efficacement face aux dangers, réduisant ainsi les risques d’accidents en entrepôt.
Bonnes pratiques en manutention et port de charges
La manutention est l’une des principales sources de risques en logistique. Un mauvais geste peut entraîner des troubles musculo-squelettiques (TMS) ou des accidents graves. Pour garantir une sécurité logistique optimale, il est essentiel d’adopter des méthodes adaptées.
- Techniques de port de charges : Privilégier une posture droite, plier les genoux plutôt que le dos et maintenir la charge près du corps pour limiter les contraintes sur la colonne vertébrale.
- Utilisation des équipements d’aide à la manutention : Encourager l’usage systématique des transpalettes, gerbeurs et chariots élévateurs pour réduire les efforts physiques.
- Rotation des tâches : Alterner les missions afin d’éviter la répétition excessive des mêmes mouvements et de limiter la fatigue musculaire.
Sécurisation des équipements et des infrastructures
Port des équipements de protection individuelle (EPI)
Les équipements de protection individuelle (EPI) sont obligatoires pour prévenir les risques liés aux chutes d’objets, aux coupures ou aux collisions. Selon le poste occupé, les salariés doivent être équipés de :
- Casques de sécurité pour se protéger contre les chutes de marchandises.
- Chaussures de sécurité renforcées pour éviter les écrasements.
- Gants de protection adaptés aux manipulations spécifiques (produits coupants, substances chimiques).
- Lunettes et masques lorsque l’activité expose à des poussières ou produits chimiques.
Les entreprises doivent mettre en place un contrôle strict et prévoir des sanctions en cas de non-port des équipements.
Entretien et contrôle des machines et outils logistiques
Un matériel bien entretenu contribue à prévenir les dysfonctionnements et les accidents. La réglementation impose des contrôles réguliers des équipements utilisés en entrepôt, notamment :
- Vérification des chariots élévateurs et transpalettes : Tests de freinage, batteries, chargeurs et état général.
- Inspection des palettiers et racks de stockage : Contrôle de la stabilité et respect des charges maximales.
- Éviter la surcharge des structures : Respecter les capacités indiquées et éviter les empilements instables.
Une maintenance préventive permet d’anticiper les risques et d’éviter les arrêts d’activité liés à des pannes ou incidents techniques.
Prévention des risques spécifiques en entrepôt
Gestion des flux et du trafic interne
Les déplacements en entrepôt sont sources de collisions et d’accidents impliquant piétons et engins de manutention. Une bonne organisation du trafic est essentielle pour éviter ces incidents :
- Mise en place de règles de priorité pour les piétons et les engins motorisés.
- Limitations de vitesse dans les zones à forte circulation.
- Signalétique et marquage au sol pour indiquer les voies de circulation.
- Installation de barrières de sécurité et de zones d’arrêt pour protéger les travailleurs.
Sécurisation des zones à risques
Certaines infrastructures présentent des dangers spécifiques nécessitant une surveillance accrue et des mesures de prévention adaptées.
Le palettier
- Les racks de stockage doivent être bien fixés et ne pas être surchargés.
- Les charges maximales doivent être affichées et respectées.
- Un contrôle quotidien doit être réalisé pour détecter d’éventuelles anomalies (montants fragilisés, échelles endommagées).
Le chariot élévateur et son cariste
- Obligation du CACES : Tout conducteur de chariot élévateur doit posséder un certificat d’aptitude (CACES) validé par une formation spécifique.
- Éviter les basculements : Les caristes doivent adapter leur vitesse et respecter les capacités de charge de l’engin.
- Sensibilisation aux risques : Le renversement du chariot et la chute de marchandises sont les accidents les plus fréquents et doivent être anticipés par des formations régulières.
Sécurité incendie et gestion des produits dangereux
La sécurité logistique inclut la prévention des risques incendie et la gestion des produits dangereux. Pour limiter ces dangers :
- Stocker les substances inflammables conformément aux normes en vigueur.
- Installer des issues de secours tous les 50 mètres et veiller à leur accessibilité.
- Vérifier régulièrement extincteurs et systèmes anti-incendie.
- Mettre en place un plan d’évacuation clair et testé périodiquement.
Assurer une sécurité logistique optimale
La sécurité logistique repose sur une organisation rigoureuse, le respect des normes et l’implication de tous les acteurs. Une bonne prévention, des formations adaptées et un entretien régulier des équipements permettent de limiter les risques et d’améliorer la productivité.
Vous souhaitez améliorer la sécurité de votre entrepôt et protéger vos équipes ? Découvrez nos machines d’emballages conçues pour optimiser la gestion logistique tout en garantissant un environnement de travail plus sûr et conforme aux normes.